Antistatic coating
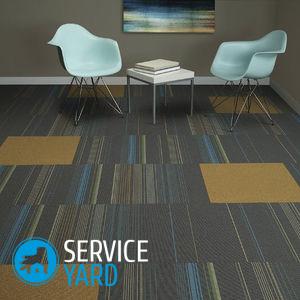
- What is it and how does antistatic coating work?
- How does antistatic coating work?
- Technological varieties of antistatic floors
- Conductive polymer antistatic bulk floors
- Screeds and cement-based bulk floors
- Antistatic paintwork
- Antistatic additives for paintwork
- Antistatic linoleums
- Rubber antistatic coatings
- Stock footage
The main and most important condition for ensuring operational safety in modern production and high-tech premises is the discharge of static charge, which can occur on the floor surface. This is due to the fact that when heterogeneous substances come into contact, as well as differences in their atomic forces, a charge arises that can disrupt or completely disable high-precision and rather expensive equipment. In this regard, most experienced professionals recommend the use of an antistatic coating, which in modern production has long been no longer an excess, but has become a mandatory operating condition.
to contents ↑What is it and how does antistatic coating work?
Antistatic flooring is a series of materials and a variety of technologies that are used together for the device of floor coverings used in industry and perform the function of removing static charges. Thanks to modern technologies, such floors can be equipped on a very wide range of substrates and have not only durable current-conducting, but also decorative properties.
Since static electricity carries a fairly large number of threats, providing protection from it is a prerequisite for such premises:
- Large computer centers, automatic telephone exchanges, server complexes, communication centers, radio and television studios. In this case, an electric charge can lead to equipment malfunctions, as a result of which important data may be lost.
- Operating and resuscitation departments in hospitals, diagnostic centers, as well as other medical institutions in which expensive high-precision equipment is installed, especially if it is responsible for the life support of seriously ill people.
- Industrial enterprises and laboratories that specialize in the production of electronic equipment.
- Due to the fact that the discharge is always accompanied by the occurrence of sparks, antistatic floors must be arranged in the rooms in which flammable substances and explosive gases are stored.
Important! Antistatic coatings do not attract dust and dirt, so they began to be widely used in children's and medical institutions, as well as in the food industry due to hygiene reasons.
In addition to production, today such a coating is used in domestic conditions.
to contents ↑How does antistatic coating work?
Static electricity is an electrical potential that appears due to free charged particles located on the surface of matter. This charge can accumulate to very impressive values, which creates the conditions for the formation of an instant discharge. In order to prevent the accumulation of a significant charge, it is necessary to create the necessary conditions on the floor surface for its outflow to the ground loop or the gradual dispersion of a natural charge into moisture in the air.Therefore, the surface of the floor must have certain conductive properties.
Important! Based on theoretical considerations, the surface should have a charge resistance of 10.4-10.9 ohms to ensure antistaticity. It is believed that the smaller the value, the more effective the protection.
Depending on the principle of their action, antistatic floors qualify for:
- Conducting, which are connected to the grounding circuit of the building.
- Not conductive. Such coatings provide an outflow of charges directly into atmospheric moisture.
Technological varieties of antistatic floors
Depending on the materials and technologies used for the manufacture of a particular coating, there are several types of antistatic floor coverings:
- Bulk with the built-in system of removal of statics;
- Paintwork materials with antistatic effect;
- Ties and self-leveling floors that prevent accumulation and ensure charge dissipation;
- Special antistatic additives in paints and varnishes;
- Linoleum with antistatic property;
- Rubber coatings.
Next, we will tell you more about each of these species.
to contents ↑Conductive polymer antistatic bulk floors
Such coatings are used in areas where even the slightest accumulation of charge should be immediately suppressed. Therefore, they have a maximum conductivity of about 10.5-10.6 ohms.
Similar systems are produced in quite a large number, most often the installation diagram for them is very similar to each other. It consists of conductive buses that are connected to a common circuit and connected to the standard ground loop of the entire building. Above they are covered with special soil, which also has electrically conductive qualities. The top layer is filled with a compound on an epoxy or polyurethane base, which contains special conductive additives.
Installation technology for conductive bulk floors
Despite the apparent simplicity and ease, the installation of such a floor should be carried out exclusively by specialists and in the following order:
- A base is being prepared, which should be at least M200 in strength under light loads, or M300 if it is planned to move a large number of people over the surface.
Important! The residual moisture content of the entire base should be 3-5%.
- The surface is cleaned of large debris, as well as dust. The base must be completely homogeneous, without any stains or residues of the old coating.
- Various irregularities and potholes with polymer-sand compositions are closed, if necessary. After the mixture has completely solidified, the surface must be sanded again.
Important! A perfectly flat rough surface is not just a decorative whim. The fact is that the thickness of the antistatic coating must be the same throughout the entire area of the room. If this criterion is not met, thickness differences can lead to differences in conductive characteristics, as a result, there is a risk of the formation of large foci of accumulation of electric charge.
- The prepared surface is coated with a special primer, which includes polymer resins. This is necessary in order to increase the adhesive properties of concrete with overlying layers.
- On top of the already dried primer, a “zero” circuit is installed, which consists of electrically conductive copper tapes.
Important! Pay attention to the fact that the layout of the stacked circuit must exactly correspond to all technological recommendations of the manufacturer.
It should also be noted that the circuit interruption is unacceptable. Therefore, copper tapes must be very close to the surface along its entire length. The resulting grid is connected to the building ground bus.
- A layer of conductive primer is applied, in which accumulation and subsequent removal of static charge will occur.
- A finishing layer is applied in the form of a self-leveling polymer coating with a decorative effect, which also has conductive properties.
to contents ↑Important! All work must be carried out very carefully, since it is simply impossible to remake or fix any area.
Screeds and cement-based bulk floors
It is possible to raise the antistatic properties of the floor by using special construction compounds in advance for filling the screed, as well as leveling the surface.
Important! Correctly selected component composition is able to provide effective dissipation of the charge that has accumulated on the surface and then drains into the surrounding atmosphere.
This coating can be arranged at home, while avoiding possible troubles that arise due to static electricity, for example, the attraction of dust and dirt. Such formulations are available in several versions at once:
- Dry mixes for screed up to 100 millimeters thick. This composition is fully operational. It is only necessary to dilute it with water to the desired consistency and fill the floor screed with the standard method.
- Dry mixes for self-leveling casting with a thickness of 5-40 millimeters. Due to the fact that this composition has fairly high adhesive properties, it can be used as a top coat.
to contents ↑Important! Such a filling of the floor does not require preliminary preparation of the base, since all the conductive qualities of this self-leveling coating are already incorporated in the component composition.
Antistatic paintwork
Absolutely any surface can be endowed with conductive properties by painting it with a special varnish or paint. These coloring compositions can be either one- or two-component, have a different degree of transparency and tinting. Such mixtures can be applied both on wooden surfaces and on concrete.
to contents ↑Important! These methods are quite primitive and insufficient for rooms with high-precision equipment, as well as enterprises with high antistatic requirements. Therefore, they are suitable exclusively for the construction of public buildings.
Antistatic additives for paintwork
If you do not have the opportunity to purchase finishing coatings with antistatic properties, you can use special additives for paint or varnish. The principle of action of such additives is to equalize the potentials in the air, as well as the surface of the floor, which subsequently leads to a drain.
Most often, such additives are made in a pasty form and are mixed with enamels or paints immediately before they are applied to the surface.
to contents ↑Antistatic linoleums
To date, the most popular are antistatic linoleums. Their conductive abilities consist in physical properties to counteract the accumulation of static charges. In addition, linoleum is also an excellent finishing decorative coating with sound and thermal insulation. In turn, antistatic linoleums are divided into three groups:
- Conducting. Their resistance is 10.6 ohms. Most often, such linoleums are used for rooms with high electrical safety requirements. The installation of this coating is quite long and complicated, reminiscent of the installation of conductive bulk floors. After the subfloor has been prepared, and the copper strips were connected to the grounding of the room, the surface is completely covered with a special conductive compound, after which linoleum itself is already covered.
Important! When laying conductive linoleum, it is very important to achieve its full fit, without the formation of air bubbles and voids under it.
- Current Dispersing.In this case, the resistance is 10.8 ohms. Such linoleums do not require a ground connection. They are uniform in thickness and include graphite microfibres in their structure. Their main advantage is the simplicity of installation, which does not require preliminary work.
- Linoleums with surface conductive qualities. Their resistance is 10.9 ohms. This coating is ideal for use in a domestic environment. By their properties, such linoleums are similar to antistatic paints and varnishes, and the laying process takes place in the most usual way.
Rubber antistatic coatings
Such coatings are rubber mats, rugs and rolled materials. Most often they were used exclusively in industrial premises and had only one color - black. Today, such products are presented in a wide range of colors. However, in everyday life they are used extremely rarely. As for the rolled material, due to its two-layer structure, it has a pronounced electrical conductivity.
to contents ↑Important! Such materials can be used with connection to the ground loop, as well as a conventional antistatic coating.
Stock footage
Regardless of the direction of the sphere of activity, the work of all modern enterprises depends solely on the working order of high-precision equipment, the malfunction or failure of which can cost not only the loss of serious information, but sometimes even human lives. Therefore, the provision and arrangement of antistatic floors for this type of enterprise is simply a necessity. In addition, such coatings also began to gain popularity in everyday life. The most important thing in this case is to select the necessary material, taking into account the level of blackout. We hope that we were able to help you understand this issue and find the right antistatic coating that can protect you from possible troubles.
- How to choose a vacuum cleaner taking into account the characteristics of the house and coatings?
- What to look for when choosing a water delivery
- How to quickly create comfort at home - tips for housewives
- How to choose the perfect TV - useful tips
- What to look for when choosing blinds
- What should be running shoes?
- What useful things can you buy in a hardware store
- Iphone 11 pro max review
- Than iPhone is better than Android smartphones