Engineering board - what is it?
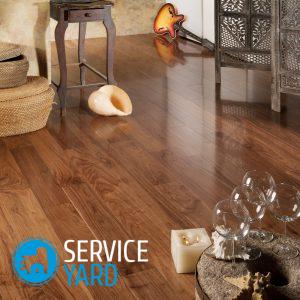
Something new is constantly appearing in the building materials market. More recently, in the everyday life of repair specialists, a new name has appeared - an engineering floor board. Consumers do not always understand this name, so they often treat this material with caution, as with any innovation. Engineering board - what is it? Let's discuss the advantages and disadvantages of this modern and very high-quality material.
to contents ↑Legends and truth
Despite the fact that the engineering board is just a floor covering, legends are already circulating about it, moreover, of the most contradictory nature. Some - ascribe almost miraculous qualities to this material, others - consider it to be something second-rate, unworthy of a solid home. In fact, in fact, these are just boards for finishing the floor, although they are made in a special way. Let's see what this coating is and how it is made.
to contents ↑Engineering board design
The flooring “engineering board” consists of two layers:
- basics;
- glued veneer.
The base is made of plywood. The thickness of the engineering board is determined precisely by the thickness of the plywood, which is usually 15 mm. For the manufacture of this layer is most often used birch. This breed has several good qualities that make it suitable for the manufacture of a multilayer material:
- plywood is durable;
- the material is slightly deformed and can withstand quite a lot of weight;
- no specific odor;
- is cheap.
Upper layer
Above, ordinary birch plywood is covered with veneer. And for him, any species of wood is used - from ordinary pine to boxwood and rosewood. This, of course, greatly affects not only the price, but also the appearance of your interior.
to contents ↑Important! Despite the fact that the engineering board appeared on sale relatively recently, manufacturers already offer quite a few of its types.
Engineering board for the floor - the pros and cons
Despite the fact that synthetic floor coverings are very popular now, many apartment owners still prefer wooden. A tree is a tree, it has a lot of advantages:
- it is a natural material that does not harm the health of households;
- wooden floors are good for any interior;
- a beautiful wooden floor gives the room a special sophistication and nobility.
Compare with parquet
If you calculate the approximate cost of a floor from an engineering board and compare with other materials, you may not really like the result. It costs more than a laminate, and especially linoleum - almost as much as a very high-quality parquet. But it is necessary to take into account the following considerations:
- The floor from the engineering board will be much stronger than the parquet.
- If we compare the parquet from valuable species and the engineering board of them, the difference in cost is very significant - by the way, manufacturers very often offer such options, while the quality increases significantly.
- Externally, the engineering board is practically no different from the floor of a solid array, but much more durable.
- The engineering board is quite simple to repair - you can putty and varnish more than once.
- The technological board is wider than the usual floor for the simple reason that it is quite difficult to find a tree from which it would be possible to cut boards half the width of the room, but plywood of this size is quite common.
- The most cardinal thing is that it is excellently suitable for underfloor heating (both electric and water), but a solid wood coating is generally not suitable for this.
Important! An engineering board has a linear expansion coefficient less than a conventional one, since the layers cancel each other out.
Disadvantages of an engineering board
This excellent modern coating, however, has some drawbacks. The manufacturers managed to get rid of the traditional flaws of the tree - due to glues and impregnations, as well as the use of high-quality plywood, the engineering board practically does not decay and does not become a breeding ground for the fungus. But you can apply it only on an almost perfect surface - any irregularities significantly reduce the quality and strength of the coating. Therefore, most often the technological board is laid already on the substrate.
to contents ↑How do they do it?
This material has another name - the technological board for the floor. To understand why she has such good qualities, you need to understand how it is made. The equipment should be modern and give great accuracy, despite the fact that the production technologies are quite traditional, and you can even say historical:
- Sawn veneer is cut, it is also a lamella, it is he who forms the upper decorative layer.
- At the same time, plywood sheets are made from 15 to 18 mm thick - by the way, quite often it is waterproof plywood, so the engineering board does not delaminate and does not rot.
- Veneer is glued onto plywood sheets, for which various PVA-based adhesives are used.
- When the panels are ready, locks are cut out on them, which will allow you to connect the boards into one array, a groove-lock is used, so the cover from the engineering board is mounted in the same way as a laminate that has already become familiar.
- The chamfer is removed.
- The panel is coated with special varnish. A UV compound is used or it is impregnated with oil with the same marking - the quality does not suffer at all from this.
- After the first, another 4-5 layers of varnish are applied.
Engineering board and humidity
The main drawback of all wooden floors is the ability to change dimensions, depending on external conditions. For example, an ordinary floorboard varies in size very significantly. If humidity decreases or increases by 1%, the board grows or shrinks by a quarter percent.
These owners of wooden floors have to deal with especially often when the house begins to heat. Humidity in the apartment falls, respectively - water, a certain amount, which is always in the wood, evaporates. The boards are reduced in size, gaps appear between them, sometimes very significant. Then the humidity increases, the boards grow again, and so every year. As a result, they first begin to creak, then dry up and lose strength.
So, this does not happen with the engineering board. Not only that, she herself has two layers, but after all, plywood is used as the basis, that is, again, multilayer material.
to contents ↑Dimensions
There are no size limits for the engineering board. The width can be quite large, 500 mm is generally the norm, so laying it is easy enough. Plus, it is an extremely simple installation, the spikes are simply inserted into the grooves, as when laying a laminate, and everything lasts for many years.
to contents ↑How to stack an engineering board?
In principle, such a coating can be in any room, even in the bathroom. Nothing prevents us from laying such a floor in the corridor, but many owners prefer to see other coatings in these rooms, for the care of which no effort is required at all.
Most often, the floor from the engineering board can be seen:
- in the living room;
- in the bedroom;
- in the nursery.
Very often, an engineering board is chosen by those who have a concrete screed made without lags.This type of coating is also convenient for basements, and in apartments it is most often laid where the “warm floor” system is made. You can mount a coating in one of two ways:
- make it floating;
- stick on.
Floating way
This option has a lot of advantages, the main of which is ease of installation:
- The installation cost is extremely low, the work itself costs almost nothing.
- You can especially not be zealous when leveling the floor - the coating will easily hide small irregularities.
- No additional hardware is needed, which also helps to reduce the total cost of work.
- You can do everything quite quickly, without having to wait until the floor dries.
- If necessary, the coating is elementarily removed and transferred to another place.
- It’s very convenient to walk on this floor.
- It is possible to evenly distribute the load over the entire area.
Important! If we are talking about small rooms, nothing else is needed. Another thing is when you were going to make the floor in a huge hall. The floating option will not be too reliable.
Adhesive method
This is a more time-consuming and costly option, but it is sometimes necessary. In addition to the engineering board itself, you will need quite a lot more:
- adhesive compositions, and they must have a high coefficient of elasticity - it is best to consult a sales assistant in a hardware store;
- tools for cutting boards, applying glue and leveling;
- high-quality base - the floor should be almost perfect, without cracks and distortions.
to contents ↑Important! Glueing the engineering board can be fixed on other bases - for example, on tile parquet, which greatly facilitates the repair, because you do not need to remove them.
Lay on the backing
A plywood substrate will help out in any situation, including when you need to mount a coating from an engineering board. Of course, in many cases, preliminary work is also necessary - the design of the subfloor, laying of thermal insulation and waterproofing, leveling, screed, and even laying pipes for the warm floor. When all this is done, you can make a substrate:
- Sheets of moisture-proof plywood 12 mm thick are laid in one or two layers on the prepared base (on concrete - one layer, on logs - in two).
- Plywood sheets are taken square, 500x500 mm or 750x750 mm.
- The drawing on the base resembles brickwork, that is, fragments are placed so that in each next row the middle of the boards fall on the seams of the previous one.
- Despite the fact that the expansion coefficient of plywood is small, it is still necessary to leave small gaps between the individual panels.
- The substrate is attached to the base with dowels with self-tapping screws.
to contents ↑Important! After the substrate is ready, it should stand without covering for five days, and only after that it will be possible to mount the panels from the engineering board.
We lay the coating
After the plywood substrate adapts to the conditions, you can lay the floors. But first you need to grind the substrate - the surface must be perfectly smooth, and plywood always has differences. Well, dirt will certainly appear in five days, it is impossible to do without it:
- Install wedges around the entire perimeter of the room so that they are at the level of future coverage. They are needed to make technological gaps between the walls and the floor - of course, the inserts must stand firmly.
- Apply glue on the back of the board - polyurethane is best. It is most convenient to do this with a notched trowel (sometimes they glue the base, or both the board and the substrate, with glue).
- If glue has got on the outside of the panel, immediately remove it, for this you always need to keep the solvent on hand.
- In addition, strengthen the boards, for which special screws or parquet nails are used.
- After gluing the panels, close the room.
- Wait about 4 days - after that it will be possible to enter the room.
Stock footage
An engineering board is an excellent modern coating that can look both modest and luxurious, depending on what style you choose.It is easy to mount, so this material has a great future.
- How to choose a vacuum cleaner taking into account the characteristics of the house and coatings?
- What to look for when choosing a water delivery
- How to quickly create comfort at home - tips for housewives
- How to choose the perfect TV - useful tips
- What to look for when choosing blinds
- What should be running shoes?
- What useful things can you buy in a hardware store
- Iphone 11 pro max review
- Than iPhone is better than Android smartphones